Seeing is Believing: Students Create Transparent Rocket Engines
Seeing is Believing: Students Create Transparent Rocket Engines
Author: | Alan Cesar |
---|
Anyone who’s seen a rocket launch knows there’s an enormous amount of light at the end of the nozzle. What happens upstream of that nozzle, however, is not often seen by human eyes. But in Purdue’s Propulsion Design, Build, and Test (DBT) course this spring, students got to do more than “just” fire their own rocket engine.
They got to see right through it.
In addition to taking a rocket engine from concept to test in just one semester, professor Tim Pourpoint challenged the students to use optically clear components as much as possible — for an unprecedented view inside.
"The idea was to have an optically clear engine, allowing us to see visible light through every part," Pourpoint explains. "That includes tanks, feed lines, cavitating venturis, valves, injectors, manifolds, injector orifices, the combustion chamber, and the nozzle."
With support from the School of Aeronautics and Astronautics, NASA, and materials supplier Formlabs, the students produced two rocket engines, developed computer models of several component in those engines, and have submitted four scientific abstracts to a major aerospace conference from their findings.
This kind of hands-on experience is a key part of the education at Purdue’s Maurice J. Zucrow Laboratories, the largest academic propulsion lab in the world.
A Clear View of Combustion
Researchers at Zucrow regularly use clear components on a small scale, through clear windows in a combustion chamber or other key components. This is not something undergraduate students typically have access to.
The class was told to default to clear materials, resorting to stainless steel and other traditional components only if absolutely necessary. Students immediately jumped to additive manufacturing for many components, finding a corporate partner to supply a special high-quality resin.
“Very quickly the students went to ‘Can we 3D-print those components out of clear plastic?’ We partnered with Formlabs on the resin, and used equipment available here on campus to print them and iterate many versions essentially at zero cost. The students printed the cavitating venturis, their orifices, and they learned how to process and machine the materials we used.”
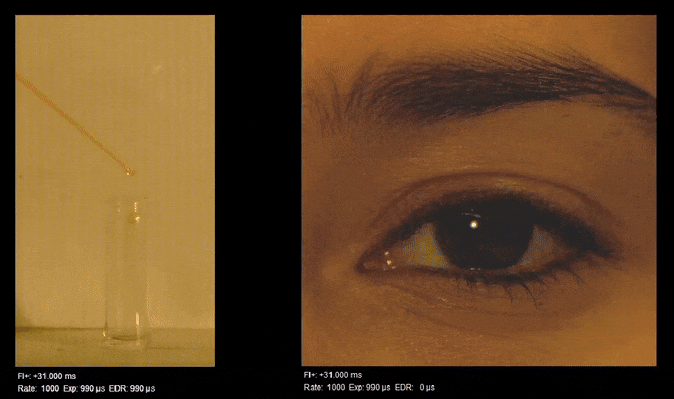
Hypergolic propulsion uses highly reactive chemicals that combust instantly on contact, many times faster than the blink of an eye.
This isn't just for show. Students also built computer models of their systems, and then compared their predictions with what they actually saw during test firing. The transparency provided a real-time view of processes like fuel cavitation and how propellants mix and burn. Watching fluids flow and ignite firsthand gives them a concrete understanding of concepts often only covered in textbooks.
Real-World Propellants and Learning from Experience
The course received outside support from both NASA's Marshall Space Flight Center and Goddard Space Flight Center, which recognized the value of students learning about optically clear combustion chambers. External funding and subject matter expertise, plus support from Purdue's School of Aeronautics and Astronautics, allowed two student teams to compete in building their transparent rocket engines.
The engines used hypergolic propellants, which ignite instantly upon contact — a crucial feature for quick maneuvers in space. Instead of the more common but highly toxic hydrazine and nitrogen tetroxide based hypergolic propellants , the class used 90% hydrogen peroxide and a low-toxicity fuel with triglyme and sodium borohydride.
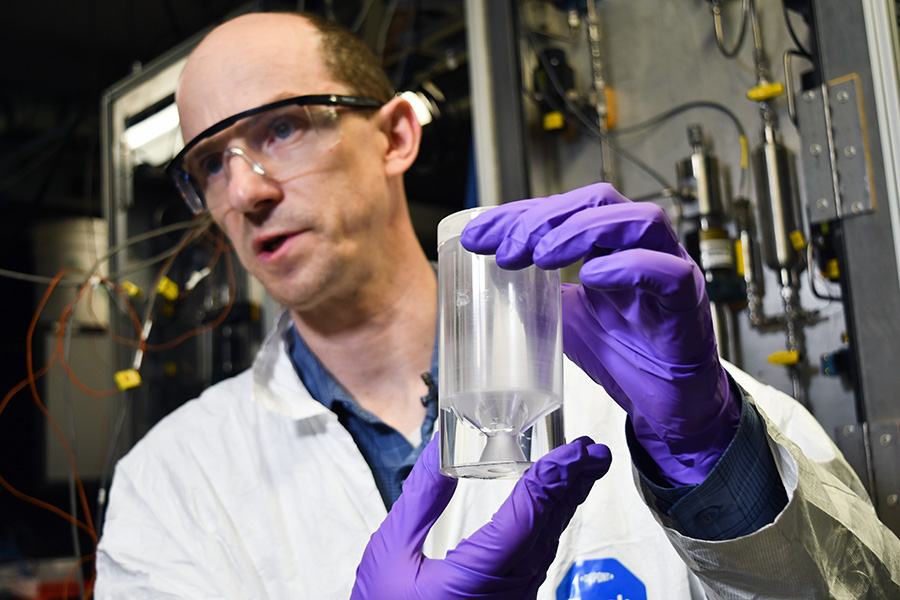
AAE Professor Tim Pourpoint holds a rocket combustion chamber made of clear sapphire. Students designed and 3D-printed many of their own clear components to meet the challenge that Pourpoint gave them in this course. Funding from NASA provided the means to have an outside company produce these delicate and strong combustion chambers from stouter materials.
An unexpected but valuable lesson came when an optically clear injector revealed a nitrogen bubble entering the oxidizer manifold, flowing down the injector and leading to combustion instability in the combustion chamber. This observation, only possible with the transparent design, turned a problem into a powerful learning moment. "It's something you don't want to see happen, but it ended up being an extremely useful thing for the students to see what it does to the combustion event,” Pourpoint points out.
Even "failures" offered insights. When the sapphire combustion chamber cracked during a test fire, one student was elated: "The cracks are exactly where we predicted they would be!"
Pourpoint added, "That was really neat; we took a risk, we wanted to see if the model was correct — and the model was correct!" This hands-on validation of their models, even under stress, is a core part of the course's teaching.
Building Skills for the Future
The skills that students gain are directly applicable to research and industry. While these 3D-printed parts won't fly on any real system, "the point is to understand how things work fundamentally and iterate on designs very quickly because we can see it, see through it," Pourpoint explains. This practical experience has already caught industry attention, with one professional asking for video of the student-designed optically-clear coaxial swirl injector to show their own engineers.
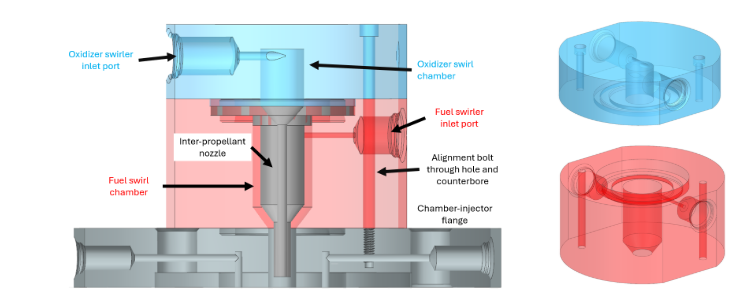
This image shows a coaxial swirl injector 3D printed using optically clear materials by one of the teams in AAE 535.
This blend of theory, rapid prototyping, and real-world testing, all in one semester, helps explain why Purdue continues to produce highly capable aerospace engineers. It's about getting hands-on, learning from every result, and truly seeing how complex systems operate.
Pourpoint's main goal is simple: "I want those students to go to their next job interview and say, 'This is how I designed it, this is how it works and this is why.' And I guarantee you they can."